|

Knit One, Pearl Two: The Art of Making Squash String
By Steve Crandall
Vice President, Sales & Marketing
Ashaway Racket Strings
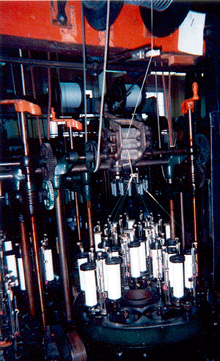
Stepping into one of our mills is like stepping through a time warp with braiders that are a fascinating example of appropriate vintage technology. Each braider has several small bobbins, arranged in two concentric circles. The core strand passes up through the middle of the circle, and the bobbins do a fast and furious dance around the core. Half of the bobbins run clockwise, and half run counterclockwise, constantly exchanging places on the inside and outside circles fast enough to make your head spin. |
We've talked a lot over the years about how using the right string can make you a better player, but we've never really talked in this column about how we actually make string. It may not be a topic that relates directly to playing squash, but it is one that surprises a lot of people. Also, having a better understanding of the string manufacturing process can give you a better understanding of the performance characteristics we try to build into it. We'll talk more about string performance next time. For now, here's how we make it.
All manufacturers like to claim that they use state-of-the-art technology in their manufacturing process, and we are no exception. Our core filaments, like high-tenacity nylon and new-age Zyex, are the absolute latest in polymer chemistry, and our coating chemistry, too, is the latest and greatest. And we utilize efficient computerized controls. What's different about making string is that "state-of-the-art" happened in the late nineteenth century! The braiding technology we use- as well as some of the machines - are over one hundred years old. No one has figured out a better way to braid string in all the years since!
Stepping into one of our mills is like stepping through a time warp (for those of you who don't know, Ashaway has been making string in this location since my great, great, great grandfather, Captain Lester Crandall, started the business in 1824 to produce commercial fishing line.) There are row upon row of clickety-clattering spinning and braiding machines all going a mile a minute. We run them with electric motors now instead of steam, but some of our machines have been producing steadily for over one hundred years.
In addition to being the only US manufacturer of racquet strings, Ashaway still manufactures cord for commercial and recreational fishing line. We are an FDA-approved supplier of medical sutures in silk and synthetic fibers, and also produce a myriad of braided cords for industrial uses, ranging from window balance cords to Jacquard loom harness twine. That FDA-level quality is built into all our products, which is one reason we have remained the quality leader in all the markets we serve.
The racquet string manufacturing process starts by twisting together strands of multifilament yarn to produce the "core" of the string. Ashaway purchases yarn bobbins in bulk from chemical companies like DuPont, and loads dozens of these onto twisting frames. Two or more strands of the hair-thin yarn are led across rollers, through guides, and onto an empty bobbin near the bottom of the machine. This bobbin spins at several thousand revolutions per minute - so fast, that you literally cannot see parts of the equipment right before your eyes. When full, the bobbin holds about 3,500 feet of twisted core.
By varying the number of twists put into the yarn for each inch of "core" produced, Ashaway is able to control the amount of elongation and resiliency we build into the string. It is through subtle, yet sophisticated measures such as this, and through careful selection of the chemical polymers of which the yarns are made, that we engineer different playing characteristics into these products.
 Through fine adjustments in machine set-up, we can engineer subtle differences in the construction of the jackets, which change the playing characteristics of the string. For example, Ashaway puts two braided cover layers - one right over the other - on its SuperNick® XL strings. |
When the twisting is complete, the core is transferred across the street to the braiding mill, where antique braiding machines put "jacket" layers over the cores. Employees wear hearing protection in the braiding room because the noise of the thousands of machines, all running at once, is a constant clattering roar.
The braiders are a fascinating example of appropriate vintage technology. Each braider has several small bobbins, arranged in two concentric circles. The core strand passes up through the middle of the circle, and the bobbins do a fast and furious dance around the core. Half of the bobbins run clockwise, and half run counterclockwise, constantly exchanging places on the inside and outside circles fast enough to make your head spin. In this way, the yarns for the covering layer are woven together over the core.
Through fine adjustments in machine set-up, we can engineer subtle differences in the construction of the jackets, which change the playing characteristics of the string. For example, Ashaway puts two braided cover layers - one right over the other - on its SuperNick® XL strings. The first, inner jacket is engineered to provide maximum protection to the core. The second, outer jacket has a more "open" pattern, for more texture and greater ball control.
In spite of the speed at which the bobbins rush around, braiding is a slow operation, yielding only about 30 inches of racquet string per minute. Subsequent processes happen a lot faster. The braided string is given a number of coatings to bind the fibers together and reduce abrasion. It is drawn through a coating bath, then shoots 40 feet straight up into a drying tower. The string may go through this process as many as six times for the right amount of coating to be applied.
Computer controlled ink-jet printers then apply the Ashaway name at some 3,000 inches per minute, then another different coating is applied to make it easier to string into racquets. Finally, the string is inspected for flaws, then metered off and cut into appropriate lengths - 30 feet for single sets and 360 feet for reels - before being packaged and shipped to your club pro and put into your racquet.
This article previously appeared in Squash Magazine.
|